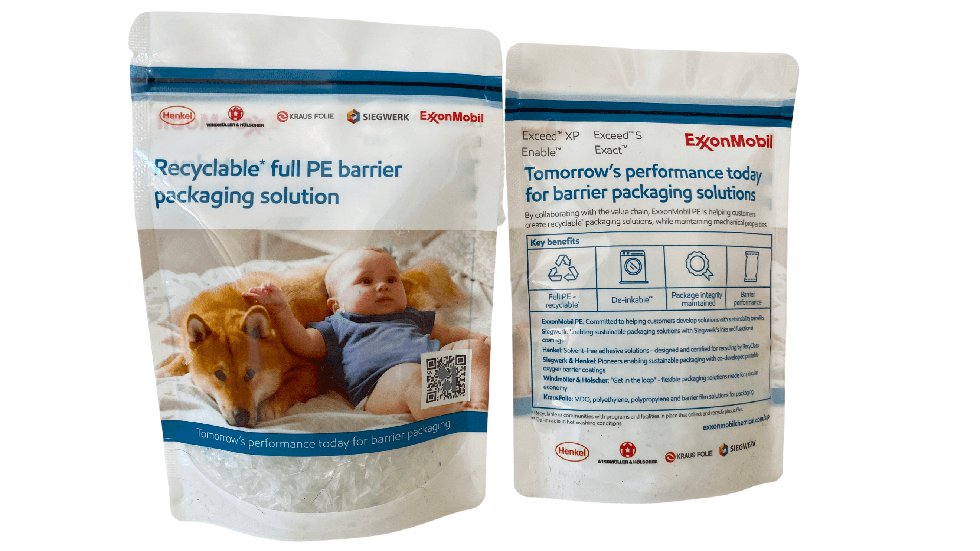
In a breakthrough development, a fully recyclable* mono-material PE pouch has been created that has similar properties to barely recyclable multi-material laminated pouches. The new pouches utilize the latest polymers, inks, functional coatings, adhesives and conversion technology and were the product of a unique value chain collaboration of ExxonMobil, Henkel, Kraus Folie, Siegwerk and Windmöller & Hölscher. The innovation allows for pouches that provide a high oxygen barrier, outstanding package integrity and excellent shelf-appeal, and produces an almost colorless recyclate after the removal of printing ink and the oxygen-barrier coating layer.
Delamination and Deinking:
In order to produce a colorless recyclate, the delamination and removal of the printing ink and coating from the laminate structure is crucial. To this end, Siegwerk´s delamination/deinking primer technology was applied on a Windmöller & Hölscher MIRAFLEX”, a flexo printing press with a downstream unit.
Depending on the requirements either solvent- (SB) or water-based (WB) primer from Siegwerk´s CIRKIT® ClearPrime product range are available. Applying industrial hot-washing conditions enables delamination and deinking of the pouch, giving an almost colorless recyclate.
High Oxygen Barrier:
Excellent oxygen barrier properties had been achieved through the use of Loctite® Liofol BC 1582 RE, a recently introduced 1-component barrier coating from Henkel, and CIRKIT® OxyBar BC 1582 from Siegwerk. The coating can be applied on both flexo and gravure presses at industrial machine speeds on various substrates, giving excellent transparency. Its compatibility with recycling has been confirmed by Cyclos HTP and it also meets Critical Guidance by American Plastic Recyclers (APR).
To match these requirements, appropriate colored and white inks from Siegwerk were used.
Laminating Adhesive:
To improve recyclability, the partners used Henkel’s new solvent-free, 2-component polyurethane laminating adhesive, LOCTITE® LIOFOL LA 7102 RE / 6902 RE. The system has been designed for mono-material structures and been recognized for its compatibility with recycling as certified by RecyClass.
Package Integrity:
Outstanding packaging integrity is achieved using ExxonMobil’s latest generation of performance polyethylene such as Exceed™ S and Exceed™ XP, in combination with Exact™ materials in the sealant layer. The MDO-PE films had been developed by ExxonMobil and Kraus Folie, employing ExxonMobil HDPE and Enable™ performance polyethylene, and produced on their VAREX” extrusion line with inline MDO unit.
Shelf Appeal:
High primer transparency combined with consistent print quality and the inherent gloss of the ExxonMobil PE-based MDO film helps to deliver an excellent shelf appeal of the final pouch. Deinking primer, print image and barrier coating had been applied in one step using a Windmöller & Hölscher MIRAFLEX” with a downstream unit.
*The terms ”recyclable” and “recyclability” as used throughout this press release are intended to refer to the potential for recyclability of full PE solutions designed and manufactured in accordance with recycling guidelines such as PRE RecyClass. Ultimate recyclability of full PE packaging will depend on a number of factors outside of the partners´ (W&H / ExxonMobil / Henkel / Siegwerk / Kraus) control including, but not limited to, availability of programs and facilities that collect and recycle plastic packaging within a given community. Any and all claims about the recyclability of full PE-packaging are the sole responsibility of the packaging manufacturer.
Partner websites: