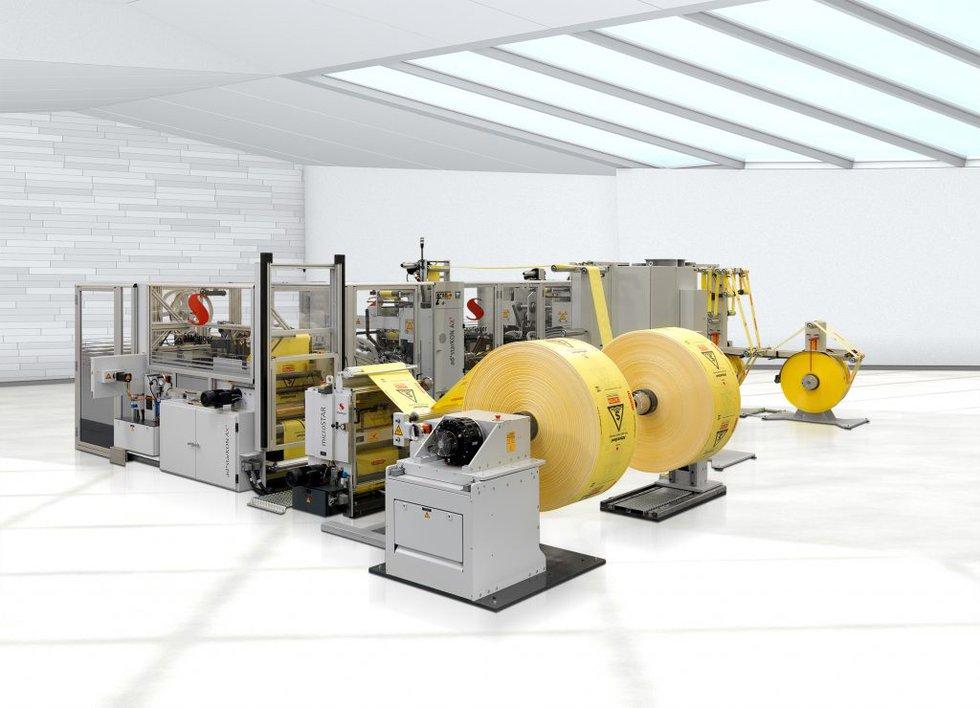
After the publication of the new National Standard for Cement Packing last October, block bottom valve bags made of coated PP tape fabric are highly sought after. Until March 2022 Chinese cement producers have to switch their packaging to one of the three cement sack types specified in the Standard. Among them: AD*STAR block bottom valve sacks made of plastic fabric, which have been developed and patented by the Austrian engineering company Starlinger.
“Since it has been established that the Starlinger AD*STAR block bottom valve sacks meet the specifications of the National Standard, demand for them in China is skyrocketing”, says Herman Adrigan, Head of Sales at Starlinger. “We are delivering conversion lines for an additional 2 billion AD*STAR sacks to China until 2022. The focus of our division Starlinger textile packaging at Chinaplas will thus be on AD*STAR production technology, although unfortunately we cannot present the latest technological developments live on a conversion line during the exhibition.”
A sustainable packaging for cement
AD*STAR block bottom valve sacks are made of laminated polypropylene tape fabric using a specially developed welding process. Contrary to blown film or kraft paper, the plastic fabric is extremely durable and break-resistant and protects the content from moisture. These characteristics make AD*STAR sacks a very sustainable cement packaging solution because they help to reduce CO2 emissions during cement production: Less cement loss caused by ruptured sacks or hardened cement in the course of the transport and logistics chain means that less cement needs to be produced for replacement – and consequently, less CO2 is emitted.
Other important advantages of AD*STAR block bottom valve bags:
- Perfectly suited for automatic filling and palletising
- The polypropylene coating ensures tightness and avoids leaking of the product
- Adjustable air permeability due to optional microperforation – reduces dust formation and protects against humidity (improved shelf life)
- Fully automated sack production on Starlinger ad*starKON conversion lines
- Attractive sack design on all visible surfaces for better brand advertising
AD*STAR block bottom valve sacks are made of laminated polypropylene tape fabric using a specially developed welding process. Contrary to blown film or kraft paper, the plastic fabric is extremely durable and break-resistant and protects the content from moisture. These characteristics make AD*STAR sacks a very sustainable cement packaging solution because they help to reduce CO2 emissions during cement production: Less cement loss caused by ruptured sacks or hardened cement in the course of the transport and logistics chain means that less cement needs to be produced for replacement – and consequently, less CO2 is emitted.
Other important advantages of AD*STAR block bottom valve bags:
- Perfectly suited for automatic filling and palletising
- The polypropylene coating ensures tightness and avoids leaking of the product
- Adjustable air permeability due to optional microperforation – reduces dust formation and protects against humidity (improved shelf life)
- Fully automated sack production on Starlinger ad*starKON conversion lines
- Attractive sack design on all visible surfaces for better brand advertising
Concentrated know-how in post-consumer plastics recycling
At this year’s Chinaplas, Starlinger recycling technology is focussing on post-consumer recycling. Be it post-consumer waste such as rigid plastic packaging, bottles, containers or films made of HDPE, PP, PE or PET – Starlinger has the recycling solution for it. In the field of PET recycling Starlinger is one of the leading technology providers: The PET regranulate produced on Starlinger lines can be used in applications with direct food contact, which has been confirmed by more than 50 positive EFSA opinions, FDA (US Food and Drug Administration) approvals as well as by various brand owners.
Starlinger also offers FDA-approved recycling solutions for the production of food grade regranulate from post-consumer HDPE packaging such as milk and beverage bottles. The regranulate can be used again in packaging for direct food contact.
No more odours in recyclates
Especially regarding post-consumer plastics, odours are a central topic. If for example HDPE packages of sanitary products are recycled, the produced regranulate frequently smells of the packaged liquids. This also often happens with LDPE post-consumer films from household and agricultural waste. Starlinger’s odour extraction technology solves this problem by removing the substances that cause the odour – because if they remain in the regranulate, unwanted smells can develop during the manufacture of new products. Starlinger C-VAC modules and odour extraction units for effective odour reduction are being used successfully in many different applications by now.
The upgrading of post-consumer regranulates with the above mentioned technologies makes it possible to close material cycles: High-quality and odour-free regranulate can effectively lead to an increased usage of recycled materials in new products.
“We develop processes and technologies to produce best quality regranulate based on more than 25 years of experience gathered in plastics recycling,” says Paul Niedl, Head of Sales of Starlinger recycling technology. “If recycled materials can replace virgin materials in part or even totally – which is the aim from a global perspective – we will have made another important step towards a circular economy.”
For more information go to www.starlinger.com or visit them at Chinaplas: 13. – 16. April 2021, Hall 10, Booth A41